Prioritizing Worker Safety: A Comprehensive Guide
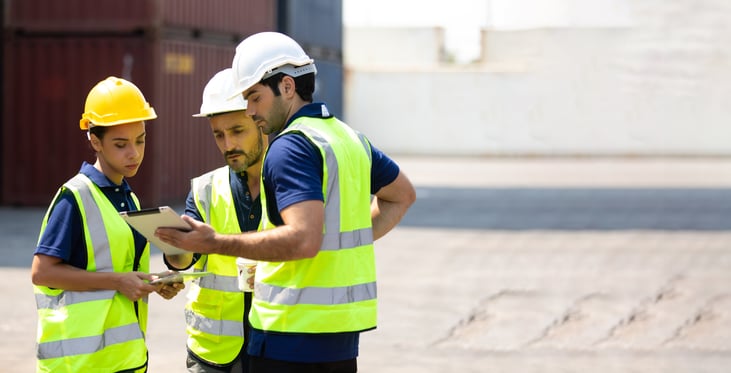
There is no such thing as being too safe at work. From providing adequate protective gear to conducting routine inspections, employers equip their workers with the necessary knowledge and skills to lessen the risk of accidents and injuries as well as lost income. The importance of effective communication strategies, safety education sessions, and the role of safety culture in creating a secure work environment cannot be overstated.
Worker Safety Through Comprehensive Training
Worker safety begins with comprehensive training and education. According to OSHA, employers who provide regular safety training to their employees can reduce workplace injury and illness rates by up to 60%. These sessions should cover topics such as hazard identification, proper use of personal protective equipment (PPE), and emergency procedures. Regular toolbox talks - brief and informal safety meetings held before the beginning of a work shift - serve as a cost-effective safety measure for refreshing workers' understanding of standard procedures. By investing in training and education, employers equip their workers with the knowledge and skills necessary to stay safe on the job, and keeps hazards at the front of every worker’s mind.
Regular Safety Inspections: Identifying Hazards
Maintenance programs and safety go hand-in-hand. Routine safety inspections are important for identifying potential hazards in the workplace. Employers should conduct careful inspections of equipment, machinery, and work areas to ensure compliance with safety standards. A well-planned maintenance program makes sure equipment is up and running, reduces accidents, reduces lost work time, and increases productivity.
Routine maintenance includes both corrective and predictive maintenance. Corrective maintenance involves immediate issues and repairs that may arise during regular use. Predictive maintenance focuses on proactive measures to prevent breakdowns before they occur. For example, using gas detectors and lockout tagout practices during inspections provides thorough coverage of possible accidents.
Promoting a Workplace Safety Culture
Fostering a safety culture creates a workplace where safety is a top priority. Effective communication plays a key role in promoting safety awareness among workers. Employers should encourage open communication channels where workers feel comfortable reporting hazards and near misses without fear of reprisal. Clarify the chain of command - when employees know what to report, they should also know who they need to report to. Display signage throughout the workplace for easily forgotten hazards, remind them what kind of PPE they need, and provide an end of shift task checklist. Regular safety meetings and toolbox talks can provide opportunities for workers to discuss safety concerns and share best practices.
Emphasizing Personal Responsibility
Workers must understand their role in maintaining a safe work environment. Employers should emphasize personal responsibility and accountability for safety. This includes actively participating in safety initiatives, following safe work practices, and wearing appropriate PPE, such as proper eye protection, head protection, and respiratory protection. Lack of concentration, an attempt to take shortcuts, or a messy and unorganized workspace are potential safety hazards. Safety is a shared responsibility that requires constant attention and commitment from everyone involved.
Continuous Improvement: Adapting Safety Practices for Ongoing Protection
Continuous evaluation and improvement of safety practices are essential for changing safety needs. Improving safety in the workplace should always be an ongoing commitment. Employers should regularly review safety protocols and seek feedback from workers to identify areas for improvement. Work with safety professionals and perform research for an assessment of your workplace's safety conditions. A different perspective and can highlight key areas for improvement. Make sure signage and training sessions are easy to follow and understand. Allow opportunities for questions to clarify any issues workers have. Take the time to find the root cause of an issue to prevent reoccurance. Reducing injuries and incidents builds feelings of safety and trust in the company, helps improve company quality, and reduces overall costs.
Common Workplace Injuries: A Brief Guide
According to NSC in 2022, the cost per worker for workplace injuries was $1,040, including the value of goods or services produced to offset the cost of injuries. Days lost due to injuries in 2022 totaled 75,000,000. Below are common workplace injuries and the products to effectively address them.
Key Takeaways
The safety of workers is paramount. By investing in training, regular inspections, effective communication, personal responsibility, and continuous improvement, employers can protect their workers from accidents and injuries. When employers emphasize safety, workers know that they are valued. Sending this message boosts morale, improves job satisfaction, and prevents financial setbacks. With the right tools, workers can perform their jobs safely and confidently, knowing that their safety is a top priority.
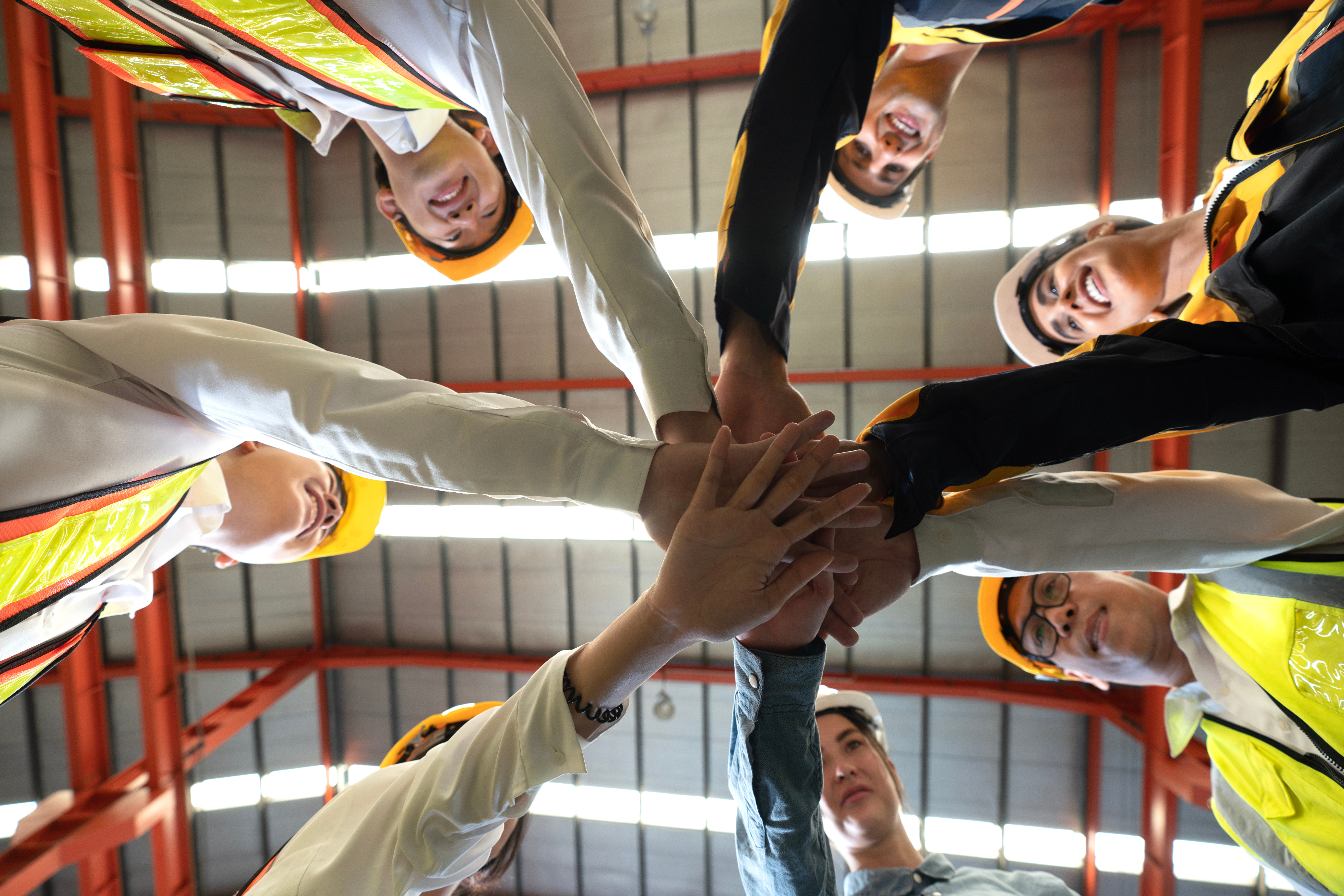
Did you know that Hantover can bring product training to you? We coordinate with vendors and industry experts to provide safety audits and product training to help make sure your facility meets compliance. Just one of the many ways we ensure the safety and well-being of your workforce.