Safety at the Loading Dock: Strategies for a Safer Warehouse Environment
In the busy environment of a warehouse, the loading dock serves as the heart of operations, where goods move in and out, and efficiency meets the relentless pace of demand. However, this hub of activity is also a focal point for workplace hazards, with a significant proportion of industrial accidents occurring within these critical zones. Ensuring safety at the loading dock not only protects workers but also ensures operational efficiency, minimizes downtime, and upholds compliance with safety regulations.
The Importance of Loading Dock Safety
A lapse in safety measures at the loading dock can have far-reaching consequences, from severe injuries to operational disruptions and legal complications. Statistics paint a stark picture, highlighting the loading dock as a hotspot for workplace accidents. It's a scenario where the cost of prevention is infinitely smaller than the cost of negligence, emphasizing the need for comprehensive safety audits and proactive risk management.
Strategies for a Secure Loading Dock
Comprehensive training for dock workers is non-negotiable. This includes familiarization with the safe operation of equipment like forklifts and pallet jacks, as well as understanding the full details of loading and unloading procedures. It is important to have quick access to any training materials, emergency guides, and Safety Data Sheets to not only improve safety but compliance as well. A well-trained team is the first line of defense against accidents.
The integrity of loading dock equipment—such as dock levelers, seals, and vehicle restraints—is crucial. Regular maintenance checks ensure these components are in top working order, preventing malfunctions that could lead to accidents. Be sure all teams that are responsible for maintenance are aware of and follow proper lockout tagout procedures as well as make sure the area is clean and free of any greases, oils or solvents once maintenance is completed.
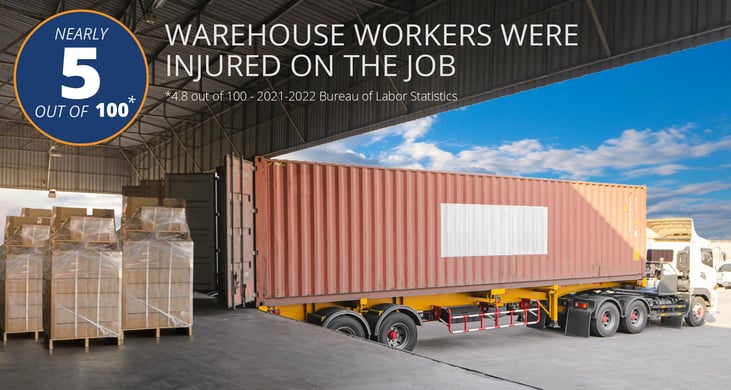
The Crucial Role of Safety Equipment for Loading Docks
By smoothing out the differences in height between the warehouse floor and the transport vehicles, dock levelers provide a solid, stable surface for moving goods. This not only minimizes the risk of accidents related to height discrepancies but also contributes to a more efficient loading and unloading process. Whether mechanical, air-powered, or hydraulic, each type of dock leveler comes equipped with unique features designed to enhance safety and operational efficiency on the loading dock.
Simple yet effective, wheel chocks play an essential role in ensuring that trailers remain stationary during the loading process. By preventing the trailer from creeping away from the dock, they help to eliminate dangerous gaps that could lead to falls or other accidents, further safeguarding workers in the vicinity.
The complexity of maintaining safety at the warehouse loading dock reflects the varied nature of warehouse operations. However, with a commitment to the strategies outlined above, bolstered by a culture of safety and continuous improvement, warehouses can significantly mitigate risks. The emphasis on training, equipment maintenance, clear communication, and preparedness forms the groundwork of a safe and efficient warehouse loading dock, underscoring the invaluable role of safety in business operations. In the final analysis, the investment in safety is an investment in the future of the warehouse, its workers, and its operational viability.